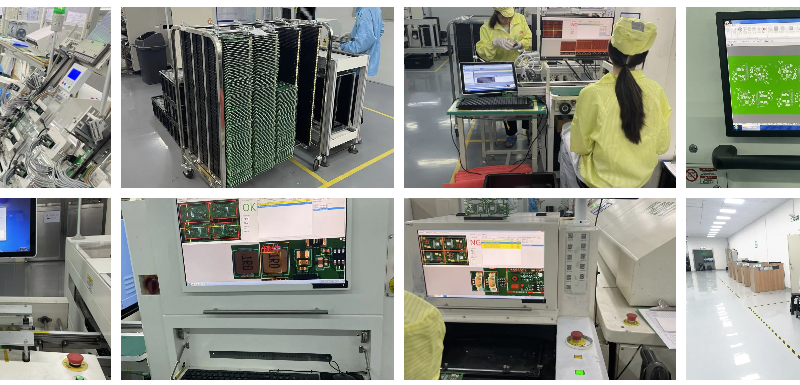
Introduction to PCB Assembly Process Flow
The PCB assembly process flow is a critical step in the manufacturing of electronic devices. It involves the careful integration of various components onto a printed circuit board (PCB), ensuring that they are correctly placed and securely connected. This process is essential for ensuring the functionality and reliability of electronic devices.
Understanding the PCB Assembly Process
To successfully navigate the PCB assembly process flow, it is important to have a clear understanding of each step involved. This guide will take you through the entire process, from PCB design and layout to final assembly and packaging. By following this step-by-step guide, you will gain valuable insights into the PCB assembly process and be better equipped to tackle any challenges that may arise.
1: PCB Design and Layout
The first step in the PCB assembly process flow is PCB design and layout. This involves designing the circuit schematic and creating a layout that determines the placement of components on the PCB. The design and layout phase is crucial as it determines the overall functionality and performance of the electronic device.
During this step, it is important to consider factors such as component placement, trace routing, and signal integrity. It is also essential to adhere to industry standards and guidelines to ensure compatibility with manufacturing processes. Once the design and layout are finalized, the PCB can move on to the next step in the assembly process.
2: Component Procurement
Component procurement is the next step in the PCB assembly process flow. It involves sourcing and acquiring the necessary components for the assembly of the PCB. This step requires careful planning and coordination to ensure that the required components are available in a timely manner.
When procuring components, it is important to consider factors such as availability, cost, and quality. It is essential to work with trusted suppliers and conduct thorough quality checks to ensure that the components meet the required specifications. Timely procurement of components is crucial to avoid delays in the assembly process.
3: PCB Fabrication
Once the components are procured, the next step in the PCB assembly process flow is PCB fabrication. This involves manufacturing the actual PCB based on the design and layout specifications. PCB fabrication typically involves processes such as layer stacking, copper etching, and solder mask application.
During the fabrication process, it is important to ensure that the PCB is manufactured to the required specifications and quality standards. This includes checking for proper layer alignment, correct trace widths, and the absence of any defects or irregularities. Once the PCB is fabricated, it is ready for the next step in the assembly process.
4: Component Placement
Component placement is a critical step in the PCB assembly process flow. It involves placing the various components onto the PCB according to the design and layout specifications. This step requires precision and accuracy to ensure that the components are correctly aligned and securely attached.
During component placement, it is important to follow the recommended guidelines for component orientation, spacing, and solderability. It is also essential to use appropriate tools and techniques to prevent damage to the components or the PCB. Once the components are placed, the PCB is ready for the next step in the assembly process.
5: Soldering and Reflow
Soldering and reflow are key steps in the PCB assembly process flow. This involves soldering the components onto the PCB to create electrical connections. Soldering can be done using various techniques such as wave soldering, selective soldering, or reflow soldering.
During the soldering process, it is important to ensure that the solder joints are properly formed and that there are no soldering defects such as solder bridges or dry joints. The temperature and time profiles during reflow soldering must be carefully controlled to prevent component damage or solder joint failures. Once the soldering and reflow process is complete, the PCB can move on to the next step in the assembly process.
6: Testing and Inspection
Testing and inspection are crucial steps in the PCB assembly process flow. These steps involve checking the functionality and quality of the assembled PCB. Testing can be done using various techniques such as automated testing, functional testing, or in-circuit testing.
During testing and inspection, it is important to check for any defects or faults such as open circuits, short circuits, or incorrect component values. It is also essential to inspect the PCB for any physical defects or irregularities. Any issues identified during testing and inspection must be resolved before proceeding to the next step in the assembly process.
7: Final Assembly and Packaging
The final step in the PCB assembly process flow is the final assembly and packaging of the electronic device. This involves integrating the assembled PCB into the final product and packaging it for shipment or distribution. The final assembly may involve additional steps such as enclosure assembly, cable routing, or firmware programming.
During the final assembly and packaging phase, it is important to ensure that all components are properly aligned and securely attached. The packaging must provide adequate protection to the electronic device during transportation and storage. Once the final assembly and packaging are complete, the electronic device is ready for use or distribution.
Common Challenges in the PCB Assembly Process
While navigating the PCB assembly process flow, there are several common challenges that may arise. These challenges include component shortages, quality issues, design errors, and manufacturing complexities. It is important to be aware of these challenges and have strategies in place to address them effectively.
To overcome component shortages, it is essential to establish strong relationships with reliable suppliers and maintain an inventory management system. Quality issues can be minimized by implementing strict quality control measures and conducting thorough inspections at each stage of the assembly process. Design errors can be avoided by conducting comprehensive design reviews and prototyping. Finally, manufacturing complexities can be managed by partnering with experienced contract manufacturers or investing in advanced equipment and technologies.
Tips for Streamlining the PCB Assembly Process
To streamline the PCB assembly process flow and improve efficiency, here are some useful tips:
- Plan and optimize the PCB layout to minimize signal interference and component placement challenges.
- Maintain clear communication and collaboration between the design, procurement, and manufacturing teams.
- Implement automated testing and inspection processes to minimize human error and improve accuracy.
- Continuously monitor and optimize the manufacturing process to identify areas for improvement and reduce cycle times.
- Invest in training and development programs to enhance the skills and knowledge of the assembly team.
- Regularly review and update the assembly process to incorporate the latest industry trends and best practices.
By following these tips, you can streamline the PCB assembly process and achieve greater efficiency and productivity.
Conclusion
Navigating the PCB assembly process flow requires a systematic approach and a clear understanding of each step involved. By following this step-by-step guide, you can effectively manage the PCB assembly process and overcome any challenges that may arise. Remember to pay attention to key factors such as design and layout, component procurement, PCB fabrication, component placement, soldering and reflow, testing and inspection, and final assembly and packaging. By implementing best practices and continuously improving the assembly process, you can achieve high-quality and reliable electronic devices.
About Fuxin
At Fuxin, we prioritize the quality by employing strict PCBA testing producre. Our commitment to a reliable and efficient testing process ensures that our products meet or exceed your quality requirements. Trust us as your EMS partner, and experience the difference of working with a manufacturer dedicated to delivering excellence.
Recent Comments